As the animal feed industry continues to evolve, automation has become increasingly important for enhancing production efficiency, improving product quality, and reducing labor costs. A well-designed automation control system is essential for the smooth and efficient operation of a 15 t/h feed mill factory. This article explores the key components and considerations involved in configuring an automation control system for a 15 t/h feed mill.
1. Programmable Logic Controllers (PLCs)
At the heart of the automation control system are programmable logic controllers (PLCs). PLCs are responsible for monitoring and controlling various processes within the feed mill, ensuring precise and consistent operation.
- PLC Selection: Choose a PLC system that is suitable for the size and complexity of the feed mill. Factors to consider include the number of input/output (I/O) points, processing speed, and memory capacity.
- PLC Programming: Develop a comprehensive PLC program that incorporates all aspects of the feed production process, including material handling, mixing, pelleting, and packaging. The program should be modular and easy to maintain, with clear documentation.
- PLC Integration: Ensure that the PLC system is seamlessly integrated with other components of the automation control system, such as HMIs, SCADA systems, and motor control centers.
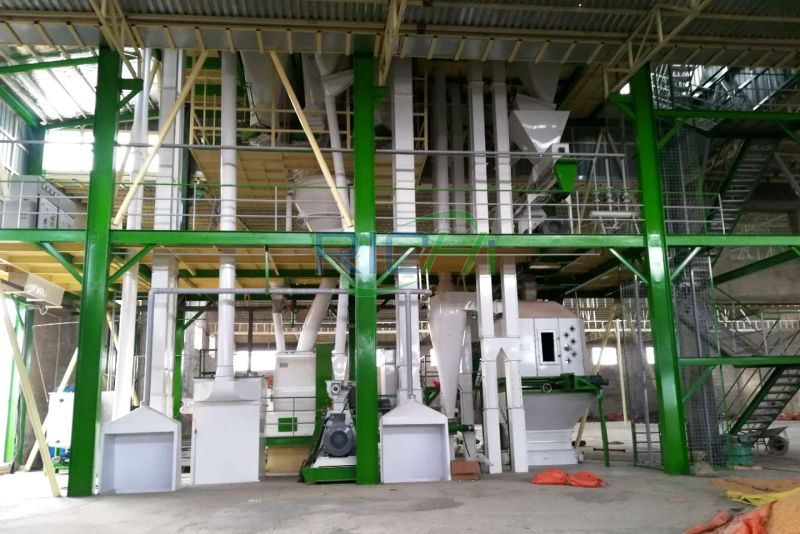
2. Human-Machine Interfaces (HMIs)
HMIs provide a user-friendly interface for operators to monitor and control the feed mill’s operations. They display real-time data on production parameters, equipment status, and alarms, allowing for quick decision-making and troubleshooting.
- HMI Selection: Choose an HMI system that is compatible with the PLC and offers features such as trending, data logging, and recipe management.
- HMI Design: Design the HMI screens to be intuitive and easy to navigate, with clear and concise information displayed. Group related data and controls together for better organization.
- HMI Security: Implement security measures, such as user access levels and passwords, to prevent unauthorized changes to the system.
3. Supervisory Control and Data Acquisition (SCADA) Systems
SCADA systems provide a higher-level of control and monitoring for the entire feed mill engineering operation. They collect data from various sources, such as PLCs and HMIs, and present it in a user-friendly format for managers and supervisors.
- SCADA Software Selection: Choose a SCADA software package that is compatible with the PLC and HMI systems and offers features such as data trending, reporting, and alarm management.
- SCADA Server Configuration: Set up the SCADA server with the appropriate hardware and software configurations to handle the data processing and storage requirements of the feed mill.
- SCADA Client Configuration: Configure SCADA client workstations with the necessary software and network settings to allow remote access and monitoring of the feed mill’s operations.
4. Motor Control Centers (MCCs)
MCCs are responsible for providing power and control to the various motors and drives used in the feed mill. They ensure that the motors operate efficiently and safely.
- MCC Selection: Choose an MCC system that is suitable for the size and power requirements of the feed mill. Factors to consider include the number of motor starters, the type of motor control (e.g., VFDs, soft starters), and the enclosure type.
- MCC Integration: Ensure that the MCC system is integrated with the PLC system for monitoring and control purposes. This allows for features such as motor overload protection, fault diagnostics, and remote control.
- MCC Layout: Design the MCC layout to be efficient and accessible, with clear labeling and documentation of the motor circuits.
5. Sensors and Instrumentation
Sensors and instrumentation are used throughout the feed mill to monitor various process parameters, such as temperature, pressure, flow, and level. These devices provide critical feedback to the automation control system for process optimization and safety.
- Sensor Selection: Choose sensors that are suitable for the specific application and environment of the feed mill. Factors to consider include accuracy, repeatability, and compatibility with the PLC system.
- Sensor Placement: Carefully plan the placement of sensors to ensure accurate and reliable measurements. Consider factors such as accessibility, interference, and environmental conditions.
- Sensor Calibration: Regularly calibrate sensors to maintain accuracy and prevent drift over time. Document the calibration procedures and results for future reference.
6. Network Infrastructure
A robust and reliable network infrastructure is essential for the effective communication and data exchange between the various components of the automation control system.
- Network Design: Design the network topology to be redundant and fault-tolerant, with multiple paths for data transmission. Use appropriate network protocols and switches to ensure reliable and secure communication.
- Network Security: Implement security measures, such as firewalls and access control lists, to protect the network from unauthorized access and cyber threats.
- Network Monitoring: Monitor the network performance and troubleshoot any issues that arise, ensuring that the system operates at optimal efficiency.
7. Operator Training and Maintenance
Proper operator training and maintenance are essential for ensuring the long-term reliability and efficiency of the automation control system.
- Operator Training: Provide comprehensive training to operators on the use and maintenance of the automation control system. This includes topics such as PLC programming, HMI navigation, and troubleshooting.
- Preventive Maintenance: Establish a preventive maintenance schedule for the automation control system, including tasks such as software updates, hardware inspections, and backup procedures.
- Documentation and Support: Maintain detailed documentation of the automation control system, including system diagrams, configuration files, and maintenance procedures. Establish a support system for addressing any issues that may arise, such as a help desk or on-site support.
Conclusion
Configuring an effective automation control system for a 15 t/h feed mill factory requires careful planning, selection of components, and integration of various systems. By incorporating PLCs, HMIs, SCADA systems, MCCs, sensors, and a robust network infrastructure, feed mill operators can enhance production efficiency, improve product quality, and reduce labor costs. However, the success of the automation control system also depends on proper operator training, preventive maintenance, and support. By investing in a well-designed and maintained automation control system, feed mill operators can stay competitive in the rapidly evolving animal feed industry.
For details please contact: pellet maker
WhatsApp:86 138 3838 9622
Email:enquiry@richipelletmachine.com