A feed pellet production line with a capacity of 10-20 tons per hour (t/h) represents a significant investment in the animal feed sector. The production capacity of such a facility has a direct impact on its sales revenue, operational efficiency, and competitive position in the market. This article delves into how the production capacity of a 10-20t/h feed pellet production line affects its sales revenue and the factors that contribute to this relationship.
Defining Production Capacity
Production capacity refers to the amount of feed a production line can generate over a specific time period. For a 10-20t/h feed pellet production line, the capacities can be outlined as follows:
- Hourly Capacity: 10-20 tons
- Daily Capacity: If the plant operates 16 hours a day, the daily capacity calculations are as follows:
- At 10t/h: 10 t/h×16 hours/day=160 tons/day10 \, \text{t/h} \times 16 \, \text{hours/day} = 160 \, \text{tons/day}10t/h×16hours/day=160tons/day
- At 20t/h: 20 t/h×16 hours/day=320 tons/day20 \, \text{t/h} \times 16 \, \text{hours/day} = 320 \, \text{tons/day}20t/h×16hours/day=320tons/day
- Annual Capacity: Assuming the plant operates 300 days a year, the annual capacity is calculated as:
- At 10t/h: 160 tons/day×300 days/year=48,000 tons/year160 \, \text{tons/day} \times 300 \, \text{days/year} = 48,000 \, \text{tons/year}160tons/day×300days/year=48,000tons/year
- At 20t/h: 320 tons/day×300 days/year=96,000 tons/year320 \, \text{tons/day} \times 300 \, \text{days/year} = 96,000 \, \text{tons/year}320tons/day×300days/year=96,000tons/year
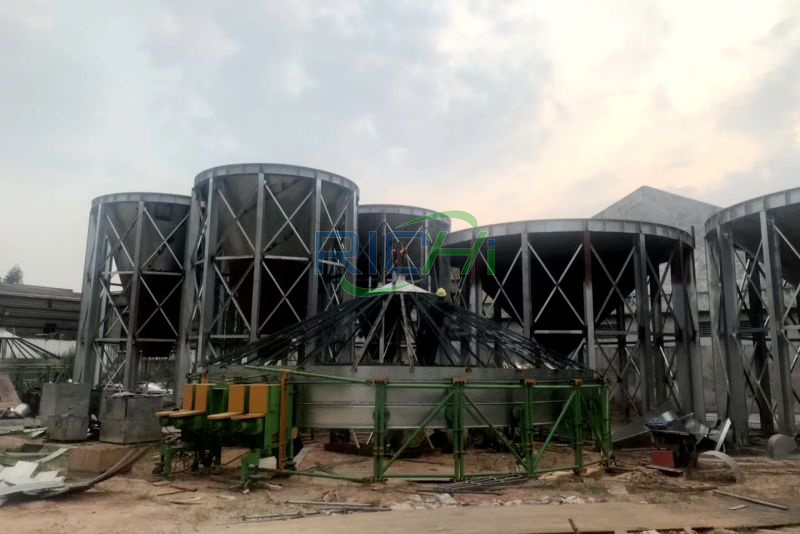
Utilization Rate
In practice, feed mills typically do not operate at maximum capacity due to maintenance, downtime, and other inefficiencies. A realistic utilization rate usually falls between 80% and 90%.
- At 80% Utilization:
- At 10t/h: 48,000 tons/year×0.80=38,400 tons/year48,000 \, \text{tons/year} \times 0.80 = 38,400 \, \text{tons/year}48,000tons/year×0.80=38,400tons/year
- At 20t/h: 96,000 tons/year×0.80=76,800 tons/year96,000 \, \text{tons/year} \times 0.80 = 76,800 \, \text{tons/year}96,000tons/year×0.80=76,800tons/year
- At 90% Utilization:
- At 10t/h: 48,000 tons/year×0.90=43,200 tons/year48,000 \, \text{tons/year} \times 0.90 = 43,200 \, \text{tons/year}48,000tons/year×0.90=43,200tons/year
- At 20t/h: 96,000 tons/year×0.90=86,400 tons/year96,000 \, \text{tons/year} \times 0.90 = 86,400 \, \text{tons/year}96,000tons/year×0.90=86,400tons/year
Average Selling Price
The selling price of animal feed varies by type and quality. For this analysis, let’s assume an average selling price of $300 per ton, a common industry benchmark for high-quality animal feed.
Calculating Annual Sales Revenue
Using the utilization rates and average selling price, we can estimate the annual sales revenue:
- At 80% Utilization:
- At 10t/h: 38,400 tons/year×$300/ton=$11,520,00038,400 \, \text{tons/year} \times \$300/\text{ton} = \$11,520,00038,400tons/year×$300/ton=$11,520,000
- At 20t/h: 76,800 tons/year×$300/ton=$23,040,00076,800 \, \text{tons/year} \times \$300/\text{ton} = \$23,040,00076,800tons/year×$300/ton=$23,040,000
- At 90% Utilization:
- At 10t/h: 43,200 tons/year×$300/ton=$12,960,00043,200 \, \text{tons/year} \times \$300/\text{ton} = \$12,960,00043,200tons/year×$300/ton=$12,960,000
- At 20t/h: 86,400 tons/year×$300/ton=$25,920,00086,400 \, \text{tons/year} \times \$300/\text{ton} = \$25,920,00086,400tons/year×$300/ton=$25,920,000
Therefore, the estimated annual sales revenue for a 10-20t/h animal feed processing plant ranges from $11.52 million to $25.92 million, depending on the utilization rate.
Factors Affecting Sales Revenue
Several factors can influence actual sales revenue, including:
- Market Demand and Price Fluctuations: Changes in demand for animal feed and corresponding price fluctuations can significantly impact revenue. High demand can raise prices, while oversupply may lead to price reductions.
- Product Mix: Different feed types (e.g., fish feed, cattle feed) come with varying price points. A diversified product range can optimize revenue by addressing different market segments.
- Operational Efficiency: Streamlined operations can boost production and minimize downtime, leading to higher effective utilization rates and revenue.
- Quality and Brand Reputation: Producing high-quality feed and maintaining a strong brand reputation can allow for premium pricing, enhancing revenue.
- Geographic Reach: Expanding sales into new regions or countries can increase market size and revenue potential.
- Sales Channels: Utilizing diverse sales channels (direct sales, distributors, retail outlets, e-commerce) can improve market penetration and revenue generation.
Example Scenario
To provide a more concrete example, consider the following scenario:
- Hourly Capacity: 15 tons
- Daily Operating Hours: 16 hours
- Annual Operating Days: 300 days
- Utilization Rate: 85%
- Average Selling Price: $320 per ton
Annual Production Calculation:
15 tons/hour×16 hours/day×300 days/year×0.85=61,200 tons/year15 \, \text{tons/hour} \times 16 \, \text{hours/day} \times 300 \, \text{days/year} \times 0.85 = 61,200 \, \text{tons/year}15tons/hour×16hours/day×300days/year×0.85=61,200tons/year
Annual Sales Revenue Calculation:
61,200 tons/year×$320/ton=$19,584,00061,200 \, \text{tons/year} \times \$320/\text{ton} = \$19,584,00061,200tons/year×$320/ton=$19,584,000
In this case, the annual sales revenue would be approximately $19.58 million.
Strategies for Optimizing Sales Revenue
To maximize sales revenue, consider implementing the following strategies:
- Enhance Product Quality: Invest in quality control processes to produce premium feed that can be sold at higher prices.
- Expand Product Range: Develop specialized, high-value feed products tailored to niche markets.
- Improve Operational Efficiency: Utilize advanced technologies and best practices to minimize downtime and enhance production efficiency.
- Strengthen Marketing Efforts: Implement targeted marketing campaigns to boost brand awareness and attract more customers.
- Leverage Technology: Use e-commerce platforms and digital marketing strategies to broaden reach and streamline sales processes.
- Build Strong Relationships: Cultivate long-term partnerships with large-scale farms, distributors, and cooperatives to ensure consistent demand.
Conclusion
The production capacity of a 10-20t/h feed pellet production line plays a crucial role in determining its sales revenue. By optimizing utilization rates, ensuring high product quality, and effectively managing operational efficiency, a feed mill can achieve substantial revenue ranging from $11.52 million to $25.92 million or more. Strategic investments in quality enhancement, operational efficiency, and market expansion can further amplify revenue potential, ensuring the long-term success and profitability of the feed mill operation.