In the competitive animal feed industry, improving production efficiency is essential for profitability and sustainability. A 10 t/h animal feed production machine is tailored to meet the needs of small to medium-scale operations, and optimizing its performance can yield substantial advantages. This article discusses effective strategies to enhance the efficiency of a 10 t/h animal feed production machine.
1. Improve Raw Material Quality
The quality of raw materials significantly influences the efficiency of feed production. High-quality ingredients lead to better feed quality and reduced waste.
- Moisture Management: Maintaining the ideal moisture content (typically 12-16%) in raw materials is crucial. Optimal moisture levels facilitate better conditioning and pelleting, improving pellet quality while lowering energy usage.
- Particle Size Optimization: Adjusting the particle size of raw materials is key for efficient mixing and pelleting. Using a hammer mill to achieve the desired particle size enhances production efficiency, as finer particles improve mixing and conditioning, resulting in higher-quality pellets.
- Ingredient Selection: Selecting high-quality ingredients with advantageous nutritional profiles enhances overall production efficiency. Ingredients with higher starch content improve pellet binding, while those with excess fiber may necessitate additional processing.
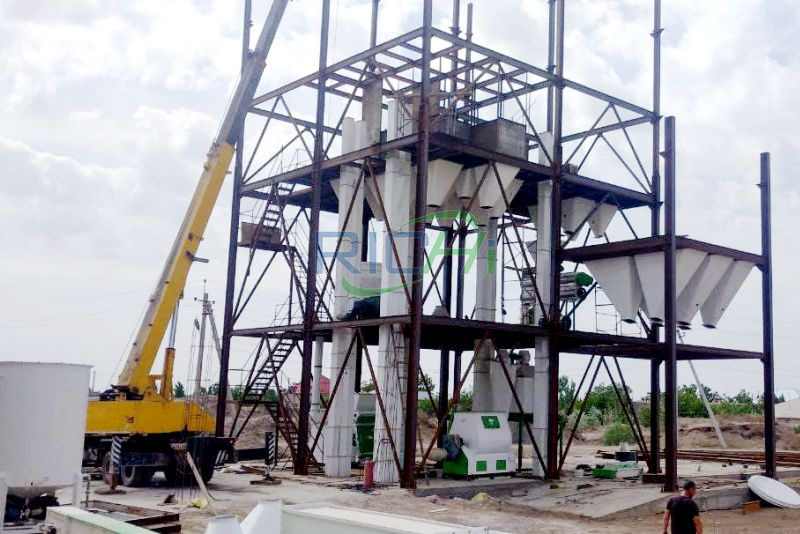
2. Upgrade Machine Design and Technology
Investing in improved machine design and advanced technology can significantly boost production efficiency.
- Advanced Pelleting Technology: Employing modern pelleting technology, such as ring die pellet mills, enhances production efficiency. Ring die mills generally provide higher output rates and better pellet quality than flat die mills, making them more suitable for larger production volumes.
- Conditioning Systems: Implementing sophisticated conditioning systems that utilize steam and moisture control can improve starch gelatinization in the feed mixture. This leads to better pellet formation and reduced energy consumption during the pelleting process.
- Automation and Control Systems: Integrating automation and control systems can optimize production processes. These advanced systems enable real-time monitoring and adjustments of critical parameters like feed rates and temperature, ensuring consistent production and minimizing waste.
3. Adopt Effective Maintenance Practices
Regular maintenance is essential for maintaining peak operational efficiency and minimizing downtime.
- Preventive Maintenance: Establish a preventive maintenance schedule based on the manufacturer’s recommendations. Routine inspections, lubrication, and replacement of worn components help prevent unexpected breakdowns and sustain consistent production levels.
- Training for Maintenance Staff: Providing training for maintenance personnel on best practices and troubleshooting techniques enhances maintenance efforts. Well-trained staff can identify potential issues early and take corrective actions to avert equipment failures.
- Monitoring Wear Components: Implementing a system to monitor the condition of wear components, such as dies and rollers, helps optimize replacement schedules and reduces the risk of production disruptions due to worn parts.
4. Streamline Production Processes
Improving production processes can lead to significant efficiency gains.
- Efficient Batching and Mixing: Implementing a streamlined batching and mixing process ensures uniformity in the feed mixture. Automated batching systems reduce manual handling and enhance accuracy, resulting in superior feed quality.
- Flow Optimization: Analyzing the production line layout to minimize material handling and transportation distances improves overall efficiency. Ensuring a smooth flow of materials from one stage to the next reduces delays and boosts throughput.
- Continuous Improvement Culture: Fostering a culture of continuous improvement within the organization leads to ongoing efficiency enhancements. Regularly reviewing production processes and seeking operator feedback helps identify areas for optimization.
5. Prioritize Energy Efficiency
Reducing energy consumption benefits both the environment and operational costs.
- Energy-Efficient Motors: Upgrading to high-efficiency motors lowers energy consumption while maintaining output levels, leading to significant long-term cost savings.
- Variable Frequency Drives (VFDs): Installing VFDs on motors allows for optimal control of speed and torque, aligning energy usage with production demands. VFDs can reduce energy consumption by enabling motors to operate at lower speeds when full power isn’t required.
- Heat Recovery Systems: Implementing heat recovery systems captures excess heat generated during pelleting and reuses it for conditioning or other purposes. This enhances energy efficiency and lowers overall production costs.
6. Maintain Quality Control and Assurance
Ensuring consistent quality in the final product is vital for customer satisfaction and regulatory compliance.
- Regular Quality Testing: Establishing a routine for testing raw materials and finished products ensures they meet nutritional and safety standards. Consistent quality checks can identify issues early, allowing for timely adjustments in the production process.
- Feedback Mechanisms: Implementing feedback systems that allow operators to report feed quality issues can pinpoint areas needing improvement. This feedback can inform adjustments to formulations and processing parameters.
- Standard Operating Procedures (SOPs): Developing and adhering to SOPs for all aspects of the production process helps maintain consistency and quality. Clear guidelines ensure all personnel follow best practices, minimizing the risk of errors.
Conclusion
Enhancing the production efficiency of a 10 t/h animal feed milling machine requires a comprehensive approach that includes optimizing raw material quality, upgrading machine design and technology, implementing effective maintenance practices, streamlining production processes, focusing on energy efficiency, and maintaining rigorous quality control.
By adopting these strategies, feed manufacturers can maximize machine output and performance, reduce operating costs, and improve the quality of the produced feed. As the demand for high-quality animal feed continues to grow, investing in these efficiency-enhancing measures will be crucial for maintaining a competitive edge in the market.
For details please contact: pelleting machine
WhatsApp:86 138 3838 9622
Email:enquiry@richipelletmachine.com