Organic fertilizer production involves several critical steps, each contributing to the overall quality and effectiveness of the final product. Among these, crushing and mixing systems serve as fundamental operations that directly impact the efficiency of production, the homogeneity of fertilizer content, and the ease of granulation. While composting and fermentation prepare the raw materials biologically, it is the crushing and mixing processes that physically refine the material, preparing it for granulation or further processing.
This comprehensive article explores the role, types, technologies, operational considerations, and benefits of crushing and mixing systems in organic fertilizer production lines.
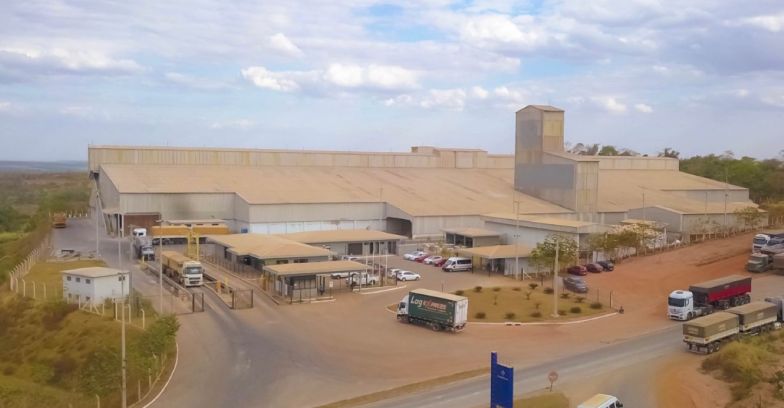
1. Overview of Crushing and Mixing in Organic Fertilizer Production
Crushing:
- Purpose: Reduce the size of organic materials (e.g., composted manure, plant waste, straw) to a uniform particle size suitable for mixing and granulation.
- When Applied: Post-composting, pre-mixing or granulation.
Mixing:
- Purpose: Uniformly blend different organic and inorganic components, ensuring even distribution of nutrients and additives throughout the material.
- When Applied: After crushing, before granulation or pelleting.
Together, these systems create a consistent, homogeneous feedstock that ensures high-quality, uniform fertilizer pellets.
2. Importance of Crushing in Fertilizer Production
Crushing may seem like a simple physical operation, but it plays a pivotal role in downstream processing.
Key Benefits:
- Improved Particle Size Distribution:
- Enhances mixing and granulation.
- Prevents clogging in granulators or pelletizers.
- Increased Surface Area:
- Facilitates better microbial interaction in residual fermentation.
- Promotes faster drying and cooling.
- Removes Large Clumps and Foreign Matter:
- Ensures the safety and reliability of equipment.
- Improves overall fertilizer texture.
- Consistency in Product Quality:
- A uniform raw material input results in consistent nutrient composition in final granules.
3. Types of Crushing Equipment
Crushing equipment selection depends on the type and moisture content of raw materials.
1. Semi-Wet Material Crusher
- Ideal for high-moisture compost materials (25%–55%).
- Uses dual rotors or hammer-type blades to crush sticky, fibrous materials.
- Advantages:
- High efficiency
- Does not clog
- Suitable for poultry manure, biogas residue, etc.
2. Straw Crusher
- Designed for crushing crop residues like wheat straw, corn stalks, and rice husks.
- Often used in combination with manure to balance C:N ratio.
- Features:
- Adjustable blades
- Dust control options
3. Chain Crusher
- Suitable for brittle materials.
- Consists of high-speed rotating chains that crush the material.
- Common Use:
- Pre-processing of urea, compost lumps
4. Vertical Crusher
- Compact design for small-scale fertilizer plants.
- Suitable for both compost and mineral materials. (Related post: fertilizer granulator machine)
4. Mixing Systems: Purpose and Process
Mixing ensures that all components of the fertilizer blend—organic base material, mineral additives (e.g., phosphate rock, potassium sulfate), binders, or microbial inoculants—are evenly distributed.
Why Mixing Matters:
- Homogeneity: Guarantees uniform nutrient availability in every granule.
- Product Consistency: Ensures each bag meets labeling and regulatory standards.
- Improved Granulation: Well-mixed material forms stronger, more uniform pellets.
5. Types of Mixers in Organic Fertilizer Lines
1. Horizontal Mixer
- Uses paddles or ribbon spirals on a horizontal shaft.
- High mixing efficiency for powder or semi-moist materials.
- Features:
- Short mixing time
- Continuous or batch operation
2. Vertical Mixer
- Vertical screw lifts materials from bottom to top.
- More suitable for small-scale operations or pre-mixing.
- Advantages:
- Compact design
- Easy maintenance
3. Double Shaft Mixer
- Two parallel shafts with paddles rotate in opposite directions.
- Suitable for sticky, high-moisture organic materials.
- Ideal For:
- Large-scale mixing
- Compost-manure blending with additives
4. Pan Mixer
- Rotating pan with fixed scraper blades.
- Offers excellent uniformity, often used in pelletizing lines.
6. Design Considerations for Crushing and Mixing Units
When designing or choosing crushing and mixing systems, the following must be considered:
Factor | Crushing Systems | Mixing Systems |
---|---|---|
Material Moisture | Choose semi-wet or wet crushers | Use paddle or double shaft mixers |
Material Type | Hardness, fiber content, clumps | Compatibility of additives and binders |
Capacity Requirements | Tons/hour of compost input | Tons/batch or tons/hour output |
Automation Level | Manual, semi-automatic, fully automatic | PLC-controlled, load cell-integrated |
Energy Consumption | Efficient motors and gearboxes | Low energy, high mixing efficiency |
Corrosion Resistance | Anti-corrosion steel or coating needed | Especially for acidic or salty materials |
7. Integration in Fertilizer Production Line
A modern organic fertilizer production line typically integrates crushing and mixing into a seamless flow:
- Post-compost material enters the crusher
- Crushed material is conveyed to the mixer
- Additives (e.g., NPK, microorganisms) are dosed into the mixer
- Mixed material proceeds to the granulator
Advanced systems include:
- Batch weighing systems for precise additive control
- Conveyor belts with sensors for real-time feed adjustment
- Dust collection systems for clean operation
8. Real-World Case Study: Cow Dung Fertilizer Plant in India
A fertilizer factory in Punjab, India processes 30 tons/day of cow dung into organic fertilizer.
System Overview:
- Crusher: Semi-wet material crusher for 50% moisture content dung
- Mixer: Horizontal ribbon mixer with PLC-controlled dosing system
- Granulation: Disc granulator
- Results:
- Increased plant efficiency by 35%
- Granule uniformity improved
- Final NPK analysis within tolerance ±2%
9. Maintenance and Operational Tips
To ensure longevity and optimal performance:
- Crusher Maintenance:
- Inspect blades weekly
- Lubricate bearings regularly
- Clean inlet to prevent blockages
- Mixer Maintenance:
- Check motor alignment and chain tension
- Clean mixing chamber after each batch
- Calibrate additive dosing regularly (Related post: 4T/H Biofertilizer Manufacturing Plant in Algeria
10. Environmental and Safety Considerations
- Dust Control: Use closed systems and dust collectors during crushing and mixing.
- Noise Management: Install noise-dampening materials and enclosures.
- Worker Safety:
- Install emergency stop buttons
- Train workers on safe material handling
- Use PPE (personal protective equipment)
11. Smart Technology Integration
Modern fertilizer factories integrate IoT and automation into these systems:
- Real-time Monitoring: Moisture sensors, temperature probes, and load cells.
- Remote Operation: Control via mobile apps or central control room.
- Data Logging: Quality control records and performance metrics.
12. Conclusion
Crushing and mixing systems are foundational components of any organic fertilizer production line. They ensure the physical and chemical uniformity of the product, support efficient granulation, and enhance the overall quality and value of the final fertilizer. Whether in a small-scale farm-based operation or a fully automated industrial line, investing in reliable crushing and mixing technology is essential for success.